Notre activité
L’utilisation du granulat
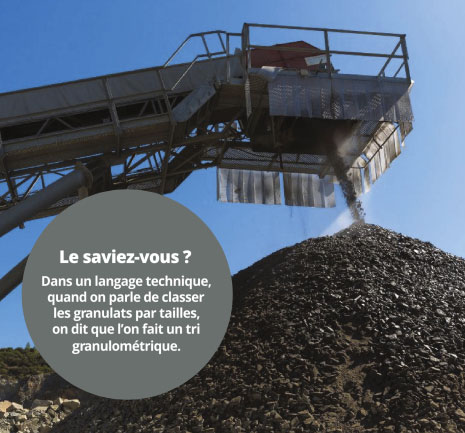
En France, la production de granulats est de l’ordre de 320 millions de tonnes par an, soit 5 tonnes par habitant.
Après l’eau, c’est la ressource la plus consommée dans le monde.
Le gisement dont la roche est extraite à la carrière de la Faubretière est composé de gneiss et d’amphibolite (roches très anciennes et formées en profondeur, il y a plusieurs centaines de millions d’années).
A partir de cette roche, l’Entreprise CHARIER CM produit différents types de granulats, sur la base de tailles standardisées, appelées “coupures”, répondants aux différents usages du secteur de la construction et des travaux publics.
En effet, ces granulats, composés de “grains” de tailles différentes, sont employés selon le type de travaux à effectuer.
La norme pour désigner les produits donne la taille des plus petits éléments puis la taille des plus gros éléments, en millimètres : d/D.
Des matériaux de grosse taille, appelés “couche de forme” et “graves”, sont par exemple utilisés pour des travaux de terrassement, les sous-couches routières ou les soubassements de bâtiments (exemples 0/150, 0/80, 0/31.5, 0/20).
Des graviers (par exemple 2/6, 6/10, 10/14, 14/20…) entrent dans la composition des bétons employés pour le gros œuvres ou pour la fabrication d’enrobés pour les routes. Ils trouvent également de nombreux emplois, à la fois fonctionnels et décoratifs, comme par exemple dans la réalisation d’allées.
Une demande locale à satisfaire
La carrière se situe à proximité de la métropole nantaise qui connaît une forte croissance démographique, conduisant à l’ouverture de nouveaux chantiers pour la construction de logements, de bureaux et d’infrastructures. La construction du nouveau CHU sur l’île de Nantes nécessite, par exemple, une grande quantité de granulats locaux et de qualité.
Il est essentiel d’avoir des ressources locales pour la réalisation de ces ouvrages. En effet, le transport représente 50 % du prix du granulat pour 30 km parcourus et celui-ci double au-delà de 50 km.
La proximité de la carrière avec les chantiers constitue donc un réel avantage économique.
De plus, cette proximité inscrit la carrière dans la transition énergétique. En effet, la carrière de La Faubretière est la carrière la plus proche de Nantes (environ 12 km) réduisant ainsi l’empreinte carbone de la Métropole dans ses besoins en granulat.
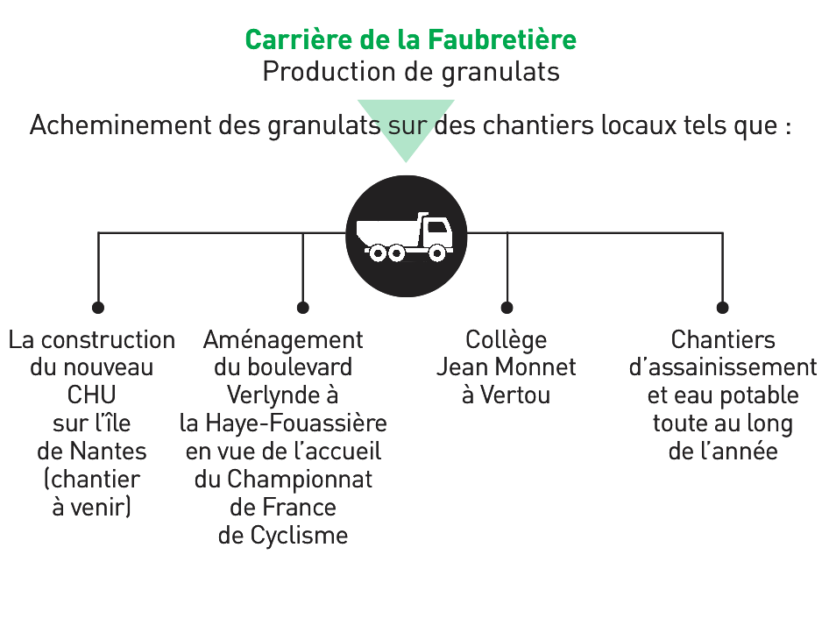
Le recyclage des granulats se développe de plus en plus, mais ne suffit pas à satisfaire la demande en quantité, ainsi qu’en qualité pour des produits aux usages spécifiques. En effet, il ne permet pas de retrouver la qualité intrinsèque initiale des granulats de carrière nécessaires à la construction d’ouvrages.
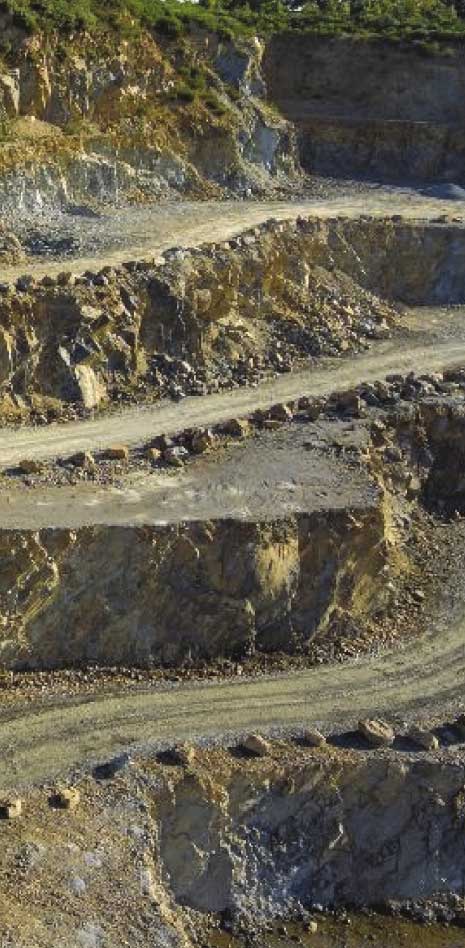
Le parcours du granulat
Qu’est-ce qu’un tir de mine ?
L’étape du minage est une étape centrale dans le processus de production du granulat. À chaque tir de mine pratiqué à la carrière de la Faubretière, c’est ainsi en moyenne 10 000 tonnes de roche massive qui sont extraites.
Il ressort par ailleurs de l’enquête effectuée en mai 2019 que les vibrations et le bruit liés aux tirs de mines arrivent en tête des gênes ressenties par les riverains (retrouvez ici tous les résultats de cette enquête).
Alors pour tout comprendre de cette étape clef de l’exploitation, nous vous proposons de découvrir en détail le déroulé d’un tir de mine.
Pour en savoir plus sur une étape, cliquez sur le pictogramme correspondant.
L’accueil de déblais inertes de chantier
En 2019, plus de 120 000 tonnes de déblais inertes de chantier ont été accueillies sur le site de la carrière de la Faubretière.
Cette activité est porteuse d’avantages notables pour le territoire, elle permet d’organiser les flux de poids lourd selon une logique de « double fret », avec des poids lourds qui arrivent avec des déchets et repartent avec des granulats.
Cela contribue à diminuer le trafic global engendré par le secteur du BTP sur la métropole nantaise, en permettant aux entreprises locales d’éviter les trajets à vide.
Cette activité de stockage des déchets inertes est très complémentaire de la production de granulat, en permettant la remise en état du site par son remblaiement progressif.
Pour en savoir plus sur chaque étape, cliquez sur le cercle correspondant:
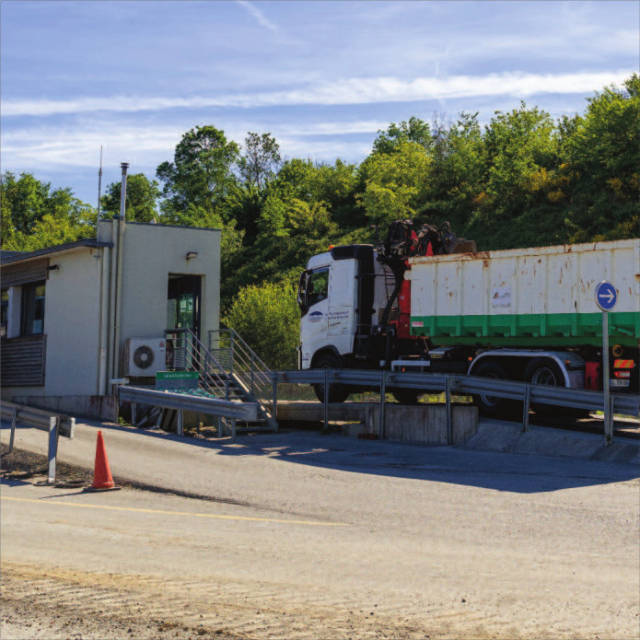
Pesée
La pesée intervient à l’entrée des camions sur le site de la carrière au moyen de la double bascule qui permet de peser en parallèle les véhicules entrants et sortants.
En sortie de carrière, le camion est pesé à vide ce qui définit le tonnage de déblais déposés
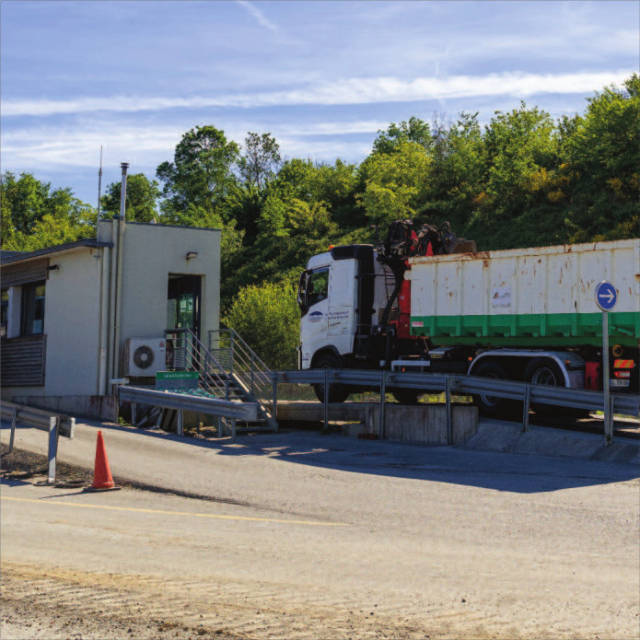
Contrôle de qualité des déblais
Le personnel en charge de l’accueil des camions procède à une vérification visuelle des matériaux composant le chargement, de façon à n’accepter que des déblais inertes.
Il vérifie également que le chargement ne comporte pas de déblais indésirables ou interdits, à savoir croûtes d’enrobés, déchets d’amiante lié, bois, plâtres, ferraille, déchets organiques, déchets dangereux, déchets radioactifs, déblais inertes non pelletables…
Le chargement n’est accepté qu’à l’issue de ce contrôle stricte.
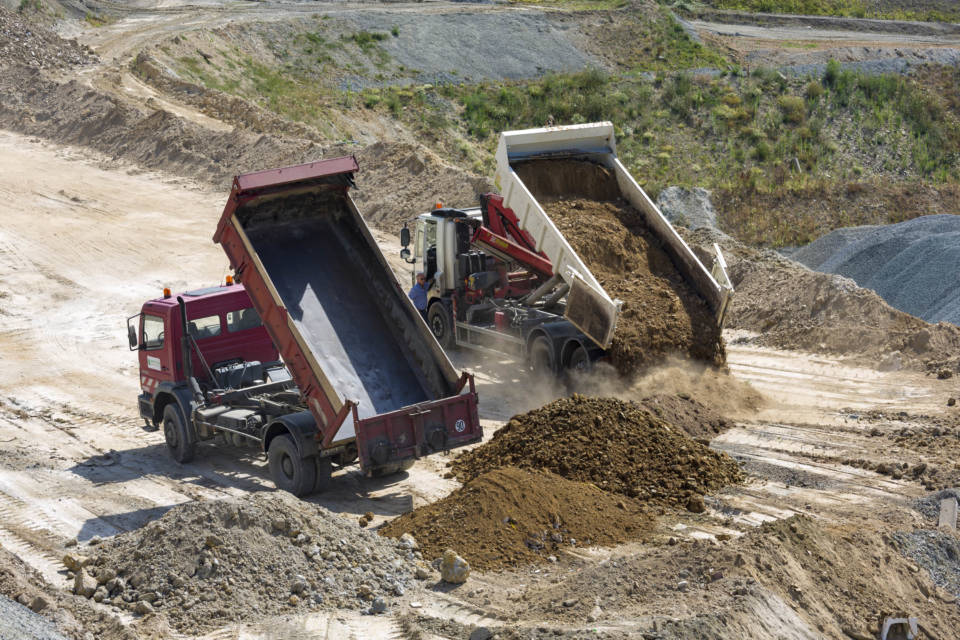
Bennage des déblais
Les camions apportant les déblais sont guidés jusqu’à l’air de déchargement, correspondant à la zone de la carrière qui fait l’objet d’une remise en état au moment du dépôt.
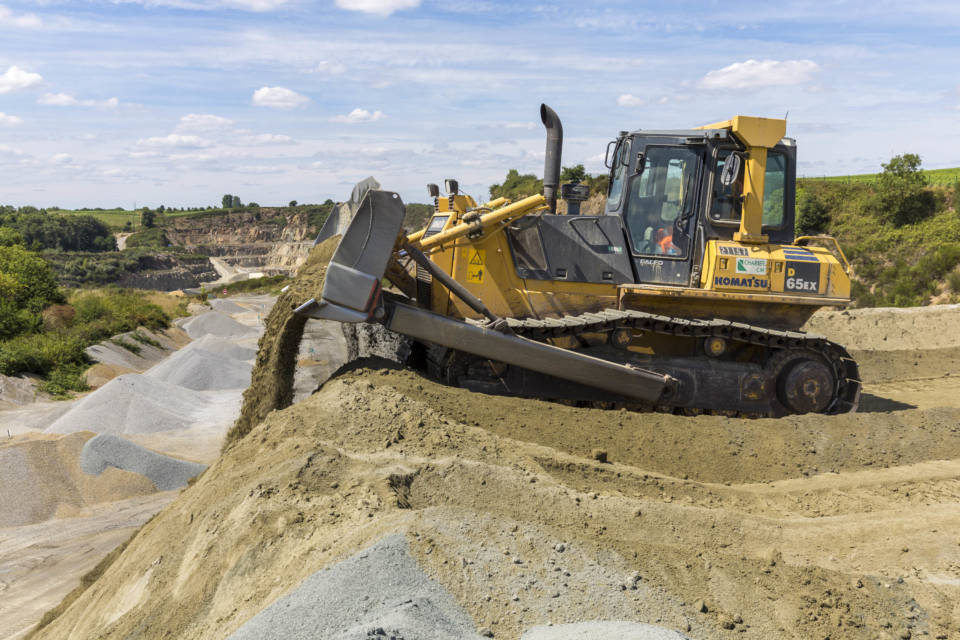
Régalage des déblais
Un bulldozer est présent sur la carrière et dédié spécifiquement à ces travaux. Il permet de déplacer les déblais, et d’aplanir les surfaces remblayées.
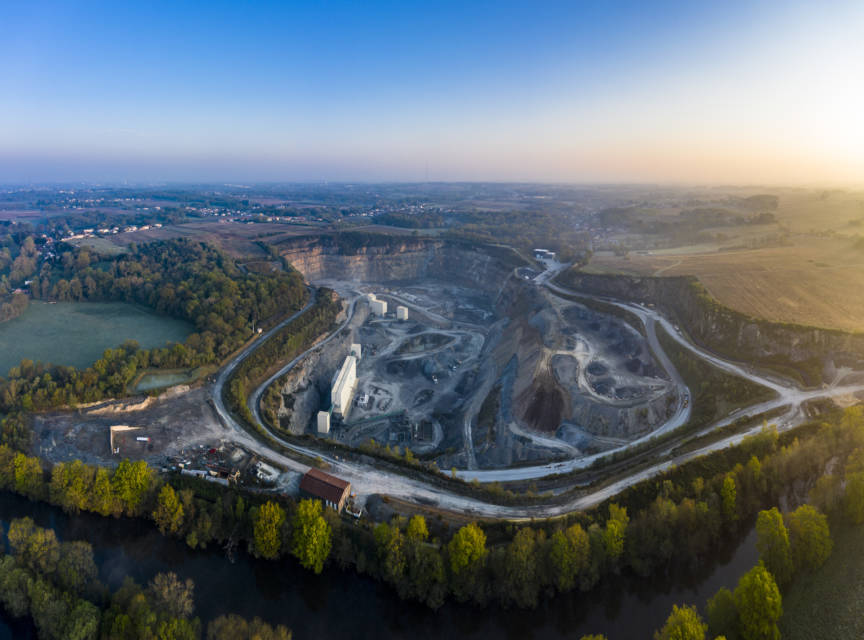
Remise en état de la carrière
La remise en état progressive du site se fait au Sud Est de l’exploitation par avancement de la zone de remblaiement au fur et à mesure des apports de déblais de chantier.